
Case
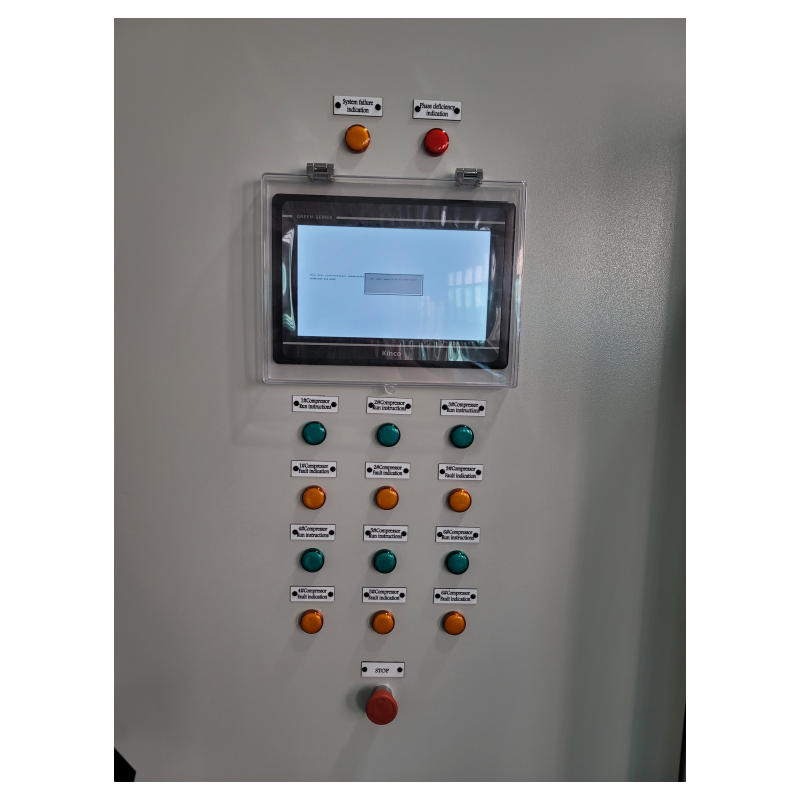
Industrial Automation Project:Automated Packaging Line in a Bakery Factory
I. Core Applications of PLC in Industrial Automation
- Production Process Control
Logic Control: Replaces traditional relays to enable automated sequential control (e.g., assembly line start/stop, workstation switching).
Motion Control: Coordinates servo and stepper motors for precise positioning (e.g., CNC machines, robotic trajectory control).
Process Control: Regulates parameters such as temperature, pressure, and flow rate (e.g., injection molding machines, heat treatment furnaces). - Machine-Level Automation
Standalone Equipment Control: Independently operates stamping machines, packaging machines, sorting systems, etc.
Safety Interlocks: Emergency stop (E-Stop), light curtain protection, safety door monitoring (compliant with ISO 13849).
3.Production Line Coordination
Multi-Equipment Synchronization: Coordinates conveyors, robotic arms, and inspection devices via industrial buses (e.g., Profinet, EtherCAT).
Flexible Manufacturing: Rapid production recipe switching (e.g., product specification changes in food processing).
- Data Acquisition & Monitoring
Real-Time Data Reporting: Transmits equipment status (current, vibration) to SCADA/MES systems.
Fault Prediction: Triggers alerts based on threshold values (e.g., motor overload).
II. Core Functions of PLC - The “Brain” of Industrial Control
- Executes deterministic control (μs-level response), ensuring precise production timing.
- High Reliability Assurance
- No mechanical contacts, lifespan exceeding 100,000 hours (far surpassing relays).
- Adaptability to Changing Needs
- Logic modifications via programming without rewiring (e.g., process adjustments).
- Standardized Interfaces
- Supports industrial communication protocols (Modbus TCP, OPC UA) for seamless device integration.
III. Key Impacts of PLC on Industrial Automation
- Revolutionizing Production Efficiency
- Automotive welding lines: PLC reduce cycle time from 60s to 30s.
- Enhanced Quality Consistency
- Eliminates human error (e.g., tightening torque accuracy within ±1%).
- Cost Optimization
- Reduces relay cabinet space and maintenance costs by over 70%.
- Enabling Smart Manufacturing
- Provides real-time data for digital twins (e.g., equipment status mapping).
IV. Future Trends in Industrial Automation - Edge Computing: PLCs locally run AI-based quality inspection models (e.g., defect detection).
- IT/OT Convergence: Tools like TIA Portal enable PLC-Python script interaction.
PLC serve as the cornerstone of industrial automation, with their evolution directly shaping the advancement of smart manufacturing.
Related projects
