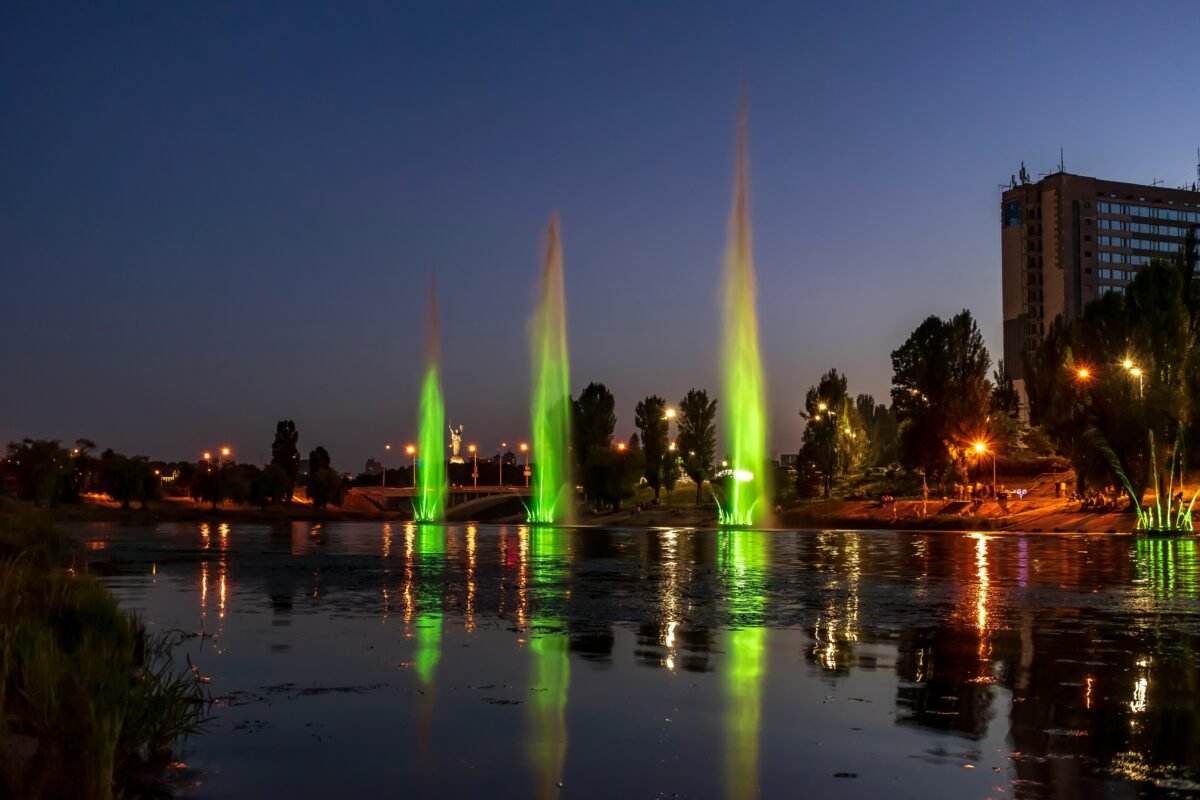
Case

Qingyuan Waterworks Project
- Control of Water Intake
Automatic start/stop of water source pumps: Controls the start and stop of intake pumps based on water level sensor data to prevent water source depletion or pump idling.Flow regulation: Adjusts the rotation speed of intake pumps or valve openings via PLC to control water intake flow, adapting to water supply demands in different periods.
- Control of Water Treatment Processes
Coagulation and sedimentation:
Automatically controls the dosage of coagulants, adjusting in real time according to parameters such as raw water turbidity and flow to ensure coagulation efficiency.
Controls the operation timing of sedimentation tank sludge scrapers and discharge valves, discharging sludge regularly to maintain sedimentation efficiency.
Filtration:
Automatically controls the backwashing process of filters (e.g., water washing, air-water backwashing), triggering backwashing based on filter differential pressure or operation time to ensure water quality.
Disinfection:
Precisely controls the dosage of disinfectants (e.g., chlorine, sodium hypochlorite), combining with online residual chlorine monitoring data to ensure effluent quality meets sanitary standards.
- Control of Clear Water Tanks and Water Supply Pump Sets
Clear water tank level management: Monitors the water level of clear water tanks in real time via PLC, automatically adjusting the operation status of inlet valves and water supply pumps to maintain stable water levels.Variable frequency control of water supply pump sets:
Adjusts the rotation speed of variable frequency pumps through PLC based on changes in pipe network pressure and water consumption to achieve constant pressure water supply, reducing pipe network leakage and energy consumption.
Coordinates the control of multiple pumps (e.g., switching between main and standby pumps) to ensure continuous water supply.
- Pipe Network Monitoring and Scheduling
Pressure and flow monitoring: Collects pressure and flow data at key points in the pipe network, transmits them to the monitoring system via PLC, and issues real-time warnings for abnormal pressure (e.g., overpressure, low pressure) to prevent pipe bursts or insufficient water supply.Remote scheduling: Supports linkage with SCADA systems to remotely adjust pipe network valve openings according to water demand in each area, optimizing water supply scheduling.
- Equipment Monitoring and Fault Handling
Operation status monitoring: Monitors parameters such as current, voltage, and temperature of pumps, fans, and dosing devices in real time, triggering automatic alarms (e.g., sound-light alarms, SMS notifications) in case of abnormalities.
Fault protection: When detecting equipment overload, short circuit, or abnormal shutdown, PLC automatically cuts off the power and starts standby equipment to reduce water outage risks.
- Data Management and Report Generation
Production data recording: Stores data such as water volume, water quality indicators, and equipment operation time, supporting historical query and trend analysis to provide a basis for process optimization.
Automated reporting: Generates daily/monthly production reports (e.g., water consumption, chemical consumption, energy consumption) to improve management efficiency.
- Energy Saving and Optimized Operation
Demand-based parameter adjustment: PLC automatically adjusts the number of operating equipment and power (e.g., variable frequency pumps, fans) according to peak/low water consumption periods to reduce energy consumption (e.g., electricity, chemical costs).
Process parameter optimization: Optimizes dosage, backwashing cycles, etc., through preset algorithms (e.g., PID control) to minimize resource waste while ensuring water quality.
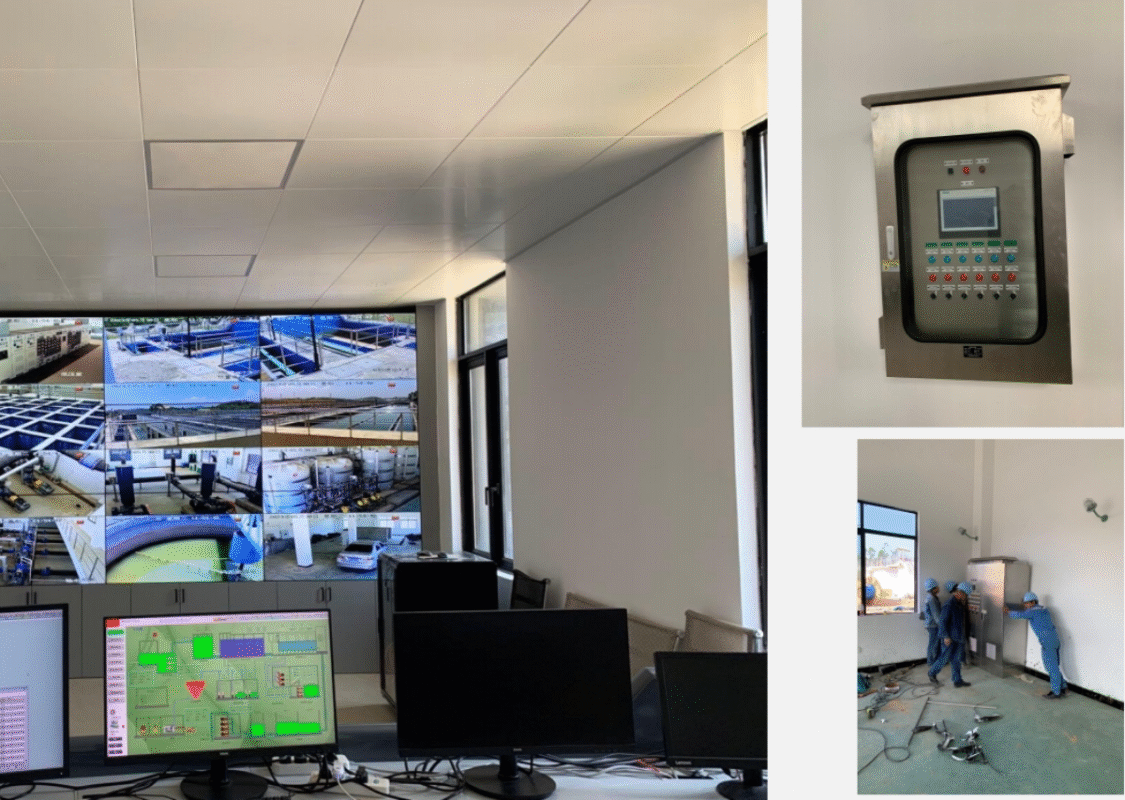
Related projects
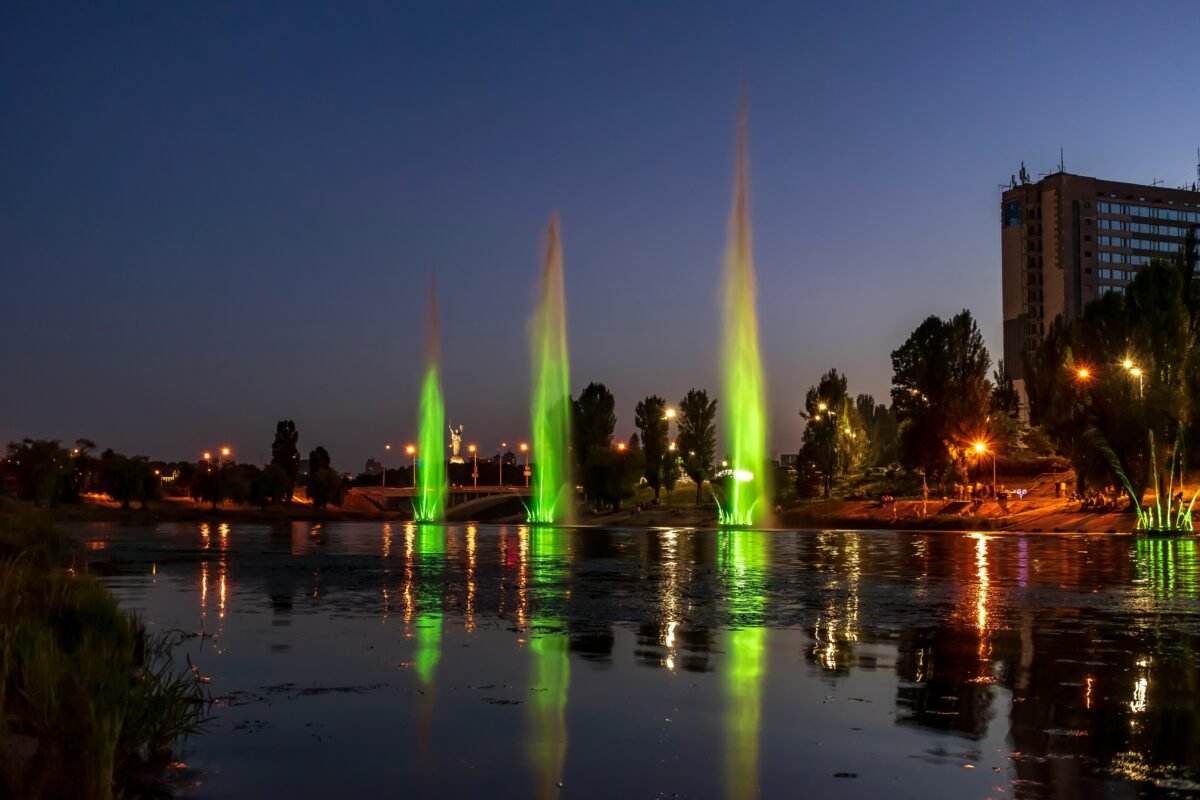